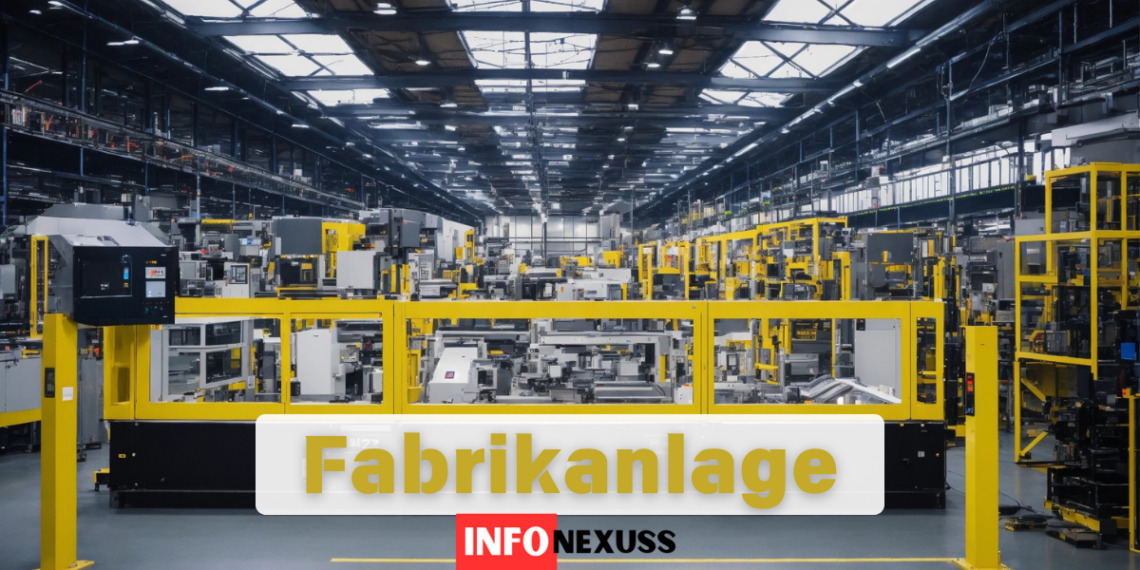
Fabrikanlage: The Future of Manufacturing
The Rise of the Fabrikanlage: A New Era in Manufacturing
The modern manufacturing landscape is a dynamic and ever-evolving arena, where innovation is the key to staying ahead of the curve. At the forefront of this revolution is the concept of the fabrikanlage, a term derived from German, which translates to “manufacturing plant” or “factory.” However, a fabrikanlage is far more than just a physical space where products are assembled; it represents a holistic, integrated approach to manufacturing that leverages cutting-edge technologies, streamlined processes, and data-driven insights to optimize efficiency, quality, and overall performance.
The fabrikanlage concept has gained significant traction in recent years as manufacturers seek to enhance their competitiveness in an increasingly globalized marketplace. By embracing the principles of the fabrikanlage, companies can unlock a myriad of benefits, ranging from reduced costs and shorter lead times to improved product quality and greater flexibility in responding to changing customer demands.
The Importance of Fabrikanlage in Modern Manufacturing
In today’s fast-paced and highly competitive business environment, the fabrikanlage has emerged as a critical driver of success for manufacturing companies across various industries. Its importance stems from its ability to address several key challenges that modern manufacturers face, including:
- The Need for Increased Efficiency: The fabrikanlage’s emphasis on lean manufacturing principles, automation, and optimized workflows enables manufacturers to streamline their operations, eliminate waste, and maximize productivity. This not only reduces costs but also allows companies to bring products to market faster, gaining a competitive edge.
- The Demand for High-Quality Products: The fabrikanlage’s focus on quality control, data-driven decision-making, and the use of advanced technologies ensures that products are consistently manufactured to the highest standards. This not only meets customer expectations but also helps to build a strong brand reputation.
- The Imperative for Flexibility: The fabrikanlage’s modular design and adaptable processes allow manufacturers to quickly respond to changing market conditions and customer preferences. This agility is crucial in a world where product lifecycles are becoming shorter and consumer demands are constantly evolving.
- The Growing Importance of Sustainability: The fabrikanlage’s commitment to resource efficiency, waste reduction, and eco-friendly manufacturing practices aligns with the growing global focus on sustainability. By adopting sustainable practices, manufacturers can not only reduce their environmental impact but also enhance their brand image and appeal to environmentally conscious consumers.
The fabrikanlage represents a paradigm shift in manufacturing, offering a comprehensive and integrated approach to optimizing production processes, enhancing product quality, and achieving sustainable growth. As the manufacturing landscape continues to evolve, the fabrikanlage is poised to play an increasingly important role in shaping the future of the industry.
What is Fabrikanlage?
A fabrikanlage is not merely a building where manufacturing takes place; it is a dynamic ecosystem that integrates cutting-edge technologies, streamlined processes, and data-driven insights to optimize every facet of production. At its core, a fabrikanlage prioritizes efficiency, quality, and adaptability, enabling manufacturers to respond swiftly to market fluctuations and customer demands. This holistic approach transcends the traditional factory model, which often operates in silos with fragmented processes and limited data integration.
Table of Contents
- 1 The Rise of the Fabrikanlage: A New Era in Manufacturing
- 2 What is Fabrikanlage?
- 3 Essential Components of a Successful Fabrikanlage
- 4 Crafting the Ideal Fabrikanlage: A Blueprint for Design Excellence
- 5 Benefits of Fabrikanlage
- 6 Navigating the Challenges of Fabrikanlage Implementation: A Realistic Perspective
- 7 Planning Your Fabrikanlage for Optimal Performance
- 8 Optimizing Your Fabrikanlage for Peak Performance
- 9 Technology and Sustainability: The Twin Engines Driving Fabrikanlage Innovation
- 10 Global Trends Revolutionizing the Fabrikanlage Landscape
- 11 Conclusion
The Evolution of the Fabrikanlage: From Traditional to Modern
The concept of the fabrikanlage has its roots in the early days of industrialization when factories first emerged as centralized production hubs. However, the traditional factory model, with its emphasis on manual labor, rigid processes, and limited automation, has gradually given way to the modern fabrikanlage.
This evolution has been driven by several factors, including:
- Technological Advancements: The advent of robotics, artificial intelligence (AI), the Internet of Things (IoT), and other Industry 4.0 technologies has revolutionized manufacturing processes. These technologies have enabled fabrikanlagen to automate repetitive tasks, collect and analyze vast amounts of data, and make real-time decisions, leading to significant improvements in efficiency, quality, and productivity.
- Globalization and Market Competition: As global competition intensifies, manufacturers are under pressure to reduce costs, improve quality, and accelerate time-to-market. The fabrikanlage, with its focus on lean manufacturing principles, continuous improvement, and agile production, provides a competitive advantage in this demanding environment.
- Changing Consumer Expectations: Today’s consumers demand high-quality, personalized products delivered quickly and at competitive prices. The fabrikanlage’s ability to customize products, optimize supply chains, and respond rapidly to changing trends enables manufacturers to meet these evolving customer expectations.
Types of Fabrikanlagen: A Spectrum of Automation and Flexibility
Fabrikanlagen can be categorized based on their level of automation and flexibility.
- Automated Fabrication: These fabrikanlagen leverage advanced robotics, AI, and IoT technologies to automate most, if not all, production processes. They are characterized by high levels of precision, consistency, and speed, making them ideal for mass production of standardized products. However, they may lack the flexibility to adapt quickly to changes in product design or demand.
- Traditional Fabrikanlagen: These facilities still rely on some manual labor but incorporate automation for specific tasks or processes. They offer a balance between automation and human intervention, allowing for greater flexibility in adapting to changing production requirements. However, they may not be as efficient as fully automated fabrikanlagen.
- Hybrid Fabrikanlagen: These are the most advanced type of fabrikanlagen, combining the best of both worlds: the efficiency and precision of automation with the flexibility and adaptability of human workers. They leverage collaborative robots (cobots) that work alongside humans, as well as AI-powered systems that optimize production processes and workflows. Hybrid fabrikanlagen are ideal for industries that require both high-volume production and the ability to customize products.
A Vision of Innovation
As technology continues to advance at an unprecedented pace, the future of the fabrikanlage is bright. We can expect to see even greater levels of automation, data integration, and intelligent decision-making in these manufacturing powerhouses. The rise of 5G networks, edge computing, and advanced analytics will further enhance the capabilities of fabrikanlagen, enabling them to operate with even greater efficiency, flexibility, and responsiveness.
Moreover, the concept of the “smart factory” is gaining momentum, where fabrikanlagen are equipped with sensors, cameras, and other IoT devices that collect and transmit real-time data on every aspect of production. This data can be analyzed to identify bottlenecks, optimize processes, predict maintenance needs, and improve overall performance.
Essential Components of a Successful Fabrikanlage
A fabrikanlage’s success hinges on the seamless integration of various key components, each playing a crucial role in achieving optimal efficiency, productivity, and quality. Understanding these components is essential for any organization seeking to establish or enhance its manufacturing capabilities.
1. Machinery: The Heart of the Fabrikanlage
At the heart of any fabrikanlage lies a sophisticated network of machinery. This includes everything from cutting-edge CNC machines, robots, and 3D printers to more traditional equipment like conveyor belts, assembly lines, and packaging machines. The selection and configuration of machinery are critical decisions that directly impact the fabrikanlage’s production capacity, flexibility, and cost-effectiveness.
Modern fabrikanlagen often incorporate “smart” machinery equipped with sensors and data collection capabilities. This allows for real-time monitoring of machine performance, predictive maintenance, and data-driven optimization of production processes. By leveraging data analytics, fabrikanlagen can identify bottlenecks, reduce downtime, and continuously improve their overall efficiency.
2. Infrastructure: The Backbone of the Fabrikanlage
The infrastructure of a fabrikanlage encompasses the physical structures and systems that support the manufacturing process. This includes the factory building itself, as well as power supply systems, transport networks, storage facilities, and waste management systems.
A well-designed infrastructure is essential for ensuring the smooth flow of materials, products, and information throughout the fabrikanlage. It should be flexible enough to accommodate changes in production volumes or product lines, and it should adhere to safety and environmental regulations.
2.1. Power Supply: Ensuring Uninterrupted Production
A reliable power supply is critical for any fabrikanlage, as even brief power outages can disrupt production and lead to costly delays. Fabrikanlagen typically have redundant power systems in place to mitigate the risk of outages, and they may also explore alternative energy sources, such as solar or wind power, to reduce their environmental footprint and energy costs.
2.2. Transport Networks: Optimizing Material Flow
Efficient transport networks are essential for moving raw materials, work-in-progress items, and finished products within the fabrikanlage. This includes conveyor systems, automated guided vehicles (AGVs), forklifts, and other material handling equipment. The layout of the transport network should be optimized to minimize travel distances, reduce bottlenecks, and ensure timely delivery of materials to production lines.
3. Workforce: The Human Element of the Fabrikanlage
While automation plays an increasingly important role in modern fabrikanlagen, the human workforce remains an indispensable component. Skilled labor is required to operate and maintain complex machinery, troubleshoot problems, and make critical decisions that cannot be fully automated.
3.1. Skilled Labor: The Driving Force of Innovation
The success of a fabrikanlage depends on a highly skilled workforce that possesses the technical expertise, problem-solving skills, and adaptability to thrive in a fast-paced manufacturing environment. Investing in employee training and development is crucial for ensuring that the workforce remains up-to-date with the latest technologies and manufacturing practices.
3.2. Training: Empowering the Workforce
Comprehensive training programs are essential for equipping employees with the knowledge and skills needed to operate and maintain the fabrikanlage’s complex machinery and systems. This includes both initial training for new hires and ongoing training to keep pace with technological advancements and changing production requirements.
The key components of a fabrikanlage – machinery, infrastructure, and workforce – are interconnected and interdependent. By ensuring that each component is optimized and functions seamlessly with the others, manufacturers can create a highly efficient, productive, and sustainable production environment. Investing in these key components is not only essential for achieving short-term goals but also for ensuring the long-term success and competitiveness of the fabrikanlage.
Crafting the Ideal Fabrikanlage: A Blueprint for Design Excellence
The design of a fabrikanlage is a multifaceted endeavor that requires meticulous planning and a comprehensive understanding of both market dynamics and production processes. A well-designed fabrikanlage is not only efficient and productive but also adaptable to changing market conditions and capable of delivering high-quality products that meet customer expectations. This section delves into the key aspects of fabrikanlage design, providing valuable insights and practical guidance for achieving optimal results.
Conceptual Planning: Laying the Foundation for Success
The conceptual planning phase is the first and arguably the most critical step in designing a fabrikanlage. It involves defining the overall vision and objectives of the facility, as well as establishing the key parameters that will guide the design process.
Market Analysis: Understanding Customer Needs and Industry Trends
A thorough market analysis is essential for identifying customer needs, preferences, and emerging trends. This information is crucial for determining the types of products that the fabrikanlage will manufacture, the target markets it will serve, and the production volumes it will need to achieve.
Identifying Customer Needs: A Customer-Centric Approach
Understanding customer needs goes beyond simply identifying the products they want. It involves delving deeper into their preferences for product features, quality, delivery times, and price points. This customer-centric approach ensures that the fabrikanlage is designed to deliver products that not only meet but exceed customer expectations.
Aligning Factory Capabilities: Matching Production with Demand
Aligning factory capabilities with market demand is a fundamental aspect of conceptual planning. This involves assessing the production capacity required to meet anticipated demand, as well as evaluating the technological capabilities needed to manufacture the desired products. By carefully aligning these factors, the fabrikanlage can be designed to operate at optimal efficiency while minimizing waste and unnecessary costs.
Layout Optimization: Maximizing Efficiency and Minimizing Waste
The layout of a fabrikanlage plays a crucial role in its overall efficiency and productivity. A well-optimized layout minimizes travel distances for materials and workers, reduces bottlenecks, and improves communication between different production areas.
Minimizing Travel Time: Streamlining Material Flow
By strategically placing workstations, storage areas, and transportation routes, a fabrikanlage can significantly reduce the time and energy spent on moving materials and products. This not only improves efficiency but also reduces the risk of damage or delays.
Reducing Bottlenecks: Identifying and Eliminating Constraints
Bottlenecks are areas in the production process where workflow is impeded, leading to delays and reduced output. By identifying and addressing these bottlenecks, a fabrikanlage can significantly improve its overall throughput and responsiveness.
Improving Communication: Facilitating Collaboration and Information Sharing
Effective communication is essential for ensuring that all departments and teams within the fabrikanlage are working in sync. A well-designed layout facilitates communication by placing related workstations in close proximity and providing ample space for meetings and collaboration.
Workflow Management: Aligning Production with Demand
Workflow management involves the coordination of tasks, resources, and information to ensure that production processes are aligned with market demand. This includes forecasting demand, scheduling production runs, managing inventory levels, and tracking the progress of orders.
Aligning Production with Demand: A Demand-Driven Approach
A demand-driven approach to production ensures that the fabrikanlage is producing the right products in the right quantities at the right time. This requires accurate demand forecasting, flexible production scheduling, and efficient inventory management. By aligning production with demand, the fabrikanlage can minimize waste, reduce inventory costs, and improve customer satisfaction.
Designing a fabrikanlage is a complex but rewarding process. By following the principles outlined in this section, manufacturers can create a facility that is not only efficient and productive but also adaptable, sustainable, and capable of delivering high-quality products that meet the ever-evolving needs of the market.
Benefits of Fabrikanlage
Investing in a fabrikanlage is a strategic decision that can yield a multitude of benefits for manufacturers. By embracing this modern approach to manufacturing, companies can unlock significant advantages that translate to increased efficiency, enhanced product quality, and reduced operational costs. Let’s delve into the key benefits that fabrikanlagen offer.
Efficiency Gains: Streamlining Processes and Interconnected Systems
One of the most significant advantages of fabrikanlagen is the substantial efficiency gains they enable. Through the integration of streamlined processes and interconnected systems, fabrikanlagen optimize every stage of production, from raw material handling to final product assembly.
Streamlined Processes: Eliminating Waste and Bottlenecks
Fabrikanlagen are designed with a focus on lean manufacturing principles, which aim to eliminate waste and streamline processes. This involves identifying and eliminating non-value-added activities, reducing unnecessary movement of materials and personnel, and optimizing the flow of information and resources. By streamlining processes, fabrikanlagen can significantly reduce lead times, improve throughput, and increase overall productivity.
Interconnected Systems: Enhancing Communication and Collaboration
Modern fabrikanlagen leverage interconnected systems that enable seamless communication and collaboration between different departments and functions. This integration allows for real-time data sharing, centralized control of production processes, and improved decision-making. By breaking down silos and fostering a collaborative environment, fabrikanlagen can respond more quickly to changes in demand, identify and address problems proactively, and continuously improve their operations.
Enhanced Product Quality: Advanced Quality Control Systems
Fabrikanlagen are equipped with advanced quality control systems that ensure consistent product quality throughout the manufacturing process. These systems leverage sensors, data analytics, and machine learning algorithms to monitor production parameters, identify deviations from specifications, and take corrective action in real time.
Advanced Quality Control Systems: Ensuring Consistency and Reducing Defects
By implementing advanced quality control systems, fabrikanlagen can significantly reduce the number of defective products, minimize rework, and improve overall product quality. This not only enhances customer satisfaction but also reduces waste and lowers production costs. Moreover, the data collected by these systems can be used to identify trends, optimize processes, and continuously improve product quality over time.
Reduced Operational Costs: Automation and Optimized Workflows
Fabrikanlagen are designed to optimize workflows and minimize operational costs. This is achieved through a combination of automation, process optimization, and data-driven decision-making.
Automation: Reducing Labor Costs and Improving Efficiency
Automation is a key component of fabrikanlagen, as it allows for the replacement of manual labor with robots and other automated systems. This not only reduces labor costs but also improves efficiency, accuracy, and consistency in production processes. Automation can be applied to various tasks, including material handling, assembly, inspection, and packaging.
Optimized Workflows: Minimizing Waste and Maximizing Productivity
In addition to automation, fabrikanlagen employ optimized workflows to minimize waste and maximize productivity. This involves carefully planning the layout of the facility, the movement of materials and personnel, and the sequence of production operations. By optimizing workflows, fabrikanlagen can reduce lead times, improve throughput, and lower overall production costs.
The benefits of fabrikanlagen are numerous and far-reaching. By embracing this modern approach to manufacturing, companies can achieve significant efficiency gains, enhance product quality, reduce operational costs, and gain a competitive edge in the global marketplace. As technology continues to advance, the potential of fabrikanlagen to transform the manufacturing industry is only set to grow.
Navigating the Challenges of Fabrikanlage Implementation: A Realistic Perspective
While the advantages of fabrikanlagen are undeniable, it’s crucial to acknowledge and address the challenges that come with their implementation. These challenges can be substantial and require careful planning and strategic decision-making to ensure a successful transition. Understanding these potential hurdles will empower businesses to make informed choices and develop effective mitigation strategies.
High Initial Investment: A Financial Hurdle
One of the most significant challenges in adopting a fabrikanlage model is the substantial initial investment required. This investment encompasses not only the acquisition of cutting-edge machinery but also the development of supporting infrastructure.
Machinery Costs: Investing in Advanced Technology
Modern fabrikanlagen rely on sophisticated machinery, such as robotic arms, automated guided vehicles (AGVs), and computer numerical control (CNC) machines. These technologies, while essential for achieving the desired levels of efficiency and precision, often come with hefty price tags. Smaller businesses or those with limited financial resources may find it challenging to secure the necessary capital for such investments.
Infrastructure Development: Building a Solid Foundation
In addition to machinery, a fabrikanlage requires a robust infrastructure to support its operations. This includes constructing or modifying facilities, installing power and utility systems, and implementing data networks and communication infrastructure. The cost of developing and maintaining this infrastructure can be considerable, especially for large-scale fabrikanlagen.
Technological Disruptions: Embracing Change and Adaptation
The rapid pace of technological advancement in the manufacturing sector presents both opportunities and challenges for fabrikanlagen. While new technologies can significantly enhance efficiency and productivity, they also require ongoing investment in upgrades and training to stay ahead of the curve.
Keeping Pace with Innovation: A Continuous Learning Process
Fabrikanlagen must be prepared to adapt to technological disruptions and embrace new innovations to remain competitive. This requires a commitment to continuous learning and a willingness to invest in training programs for employees. Additionally, companies must carefully evaluate the potential benefits and risks of new technologies before implementing them, ensuring that they align with the overall goals and objectives of the fabrikanlage.
Regulatory Constraints: Navigating the Legal Landscape
Fabrikanlagen must comply with a wide range of regulations related to safety, environmental protection, and labor laws. These regulations can vary significantly across different regions and industries, adding another layer of complexity to the implementation process.
Compliance and Risk Management: Ensuring Legal and Ethical Operations
Staying abreast of evolving regulatory requirements and ensuring compliance is crucial for the smooth operation of a fabrikanlage. Non-compliance can result in fines, legal disputes, and reputational damage. Therefore, it is essential for companies to have robust risk management strategies in place to identify and mitigate potential regulatory risks.
Overcoming Challenges: Strategies for Success
While the challenges associated with fabrikanlagen are significant, they are not insurmountable. By adopting a proactive and strategic approach, companies can overcome these hurdles and reap the substantial rewards that this innovative manufacturing model offers.
- Financial Planning: Developing a comprehensive financial plan that accounts for both the initial investment and ongoing operational costs is essential. This may involve securing funding through loans, grants, or equity investments.
- Technology Roadmap: Creating a technology roadmap that outlines the planned adoption and integration of new technologies can help ensure that the fabrikanlage remains at the forefront of innovation.
- Regulatory Compliance: Establishing a dedicated compliance team or partnering with external experts can help ensure that the fabrikanlage adheres to all relevant regulations and standards.
- Employee Training: Investing in comprehensive training programs for employees is crucial for ensuring that they have the skills and knowledge needed to operate and maintain the fabrikanlage’s complex systems.
By addressing these challenges head-on and implementing effective mitigation strategies, companies can successfully navigate the path to fabrikanlage implementation and unlock its full potential for transforming their manufacturing operations.
Planning Your Fabrikanlage for Optimal Performance
The journey towards establishing a successful fabrikanlage begins with meticulous planning. This phase lays the groundwork for a facility that not only meets current demands but is also adaptable to future market fluctuations and technological advancements. A comprehensive plan encompasses three key pillars: market analysis, resource allocation, and production forecasting.
Aligning Production with Demand
A comprehensive market analysis is the cornerstone of fabrikanlage planning. It involves delving into the intricacies of your target market, understanding consumer preferences, identifying emerging trends, and assessing the competitive landscape. This in-depth understanding allows you to tailor your production capabilities to meet the specific needs and demands of your customers.
By analyzing market data, you can gain valuable insights into:
- Product Demand: This involves identifying the types of products that are in high demand, their expected sales volumes, and their projected growth rates. This information is crucial for determining the scale of your fabrikanlage and the production capacity required to meet market demand.
- Customer Preferences: Understanding customer preferences regarding product features, quality, and price points is essential for designing products that resonate with your target audience. This information can guide decisions on product design, materials selection, and production processes.
- Competitive Landscape: Assessing the strengths and weaknesses of your competitors can help you identify opportunities for differentiation and innovation. This can inform your product development strategy, pricing strategy, and marketing efforts.
Optimizing Efficiency and Minimizing Waste
Resource allocation is a critical aspect of fabrikanlage planning that involves determining the optimal allocation of resources, including capital, labor, and materials. The goal is to maximize efficiency, minimize waste, and ensure that all resources are utilized effectively.
Effective resource allocation involves:
- Capacity Planning: Determining the optimal production capacity of your fabrikanlage based on market demand forecasts and production capabilities.
- Equipment Selection: Choosing the right machinery and equipment that aligns with your production goals and budget constraints.
- Material Management: Implementing strategies for efficient procurement, storage, and utilization of raw materials and components.
- Workforce Planning: Determining the number and skillset of employees required to operate and maintain the fabrikanlage, as well as developing training programs to ensure their competence.
By carefully allocating resources, you can ensure that your fabrikanlage operates at peak efficiency, minimizing downtime and maximizing output.
Anticipating Future Demand
Production forecasting involves predicting future demand for your products based on historical data, market trends, and other relevant factors. Accurate production forecasting is essential for aligning production with demand, avoiding overproduction or underproduction, and ensuring optimal inventory levels.
Modern fabrikanlagen often employ sophisticated forecasting models that incorporate data from various sources, such as sales data, market research, and economic indicators. These models can help you anticipate fluctuations in demand, plan production schedules accordingly, and make informed decisions about inventory management.
The planning phase of a fabrikanlage project is a critical investment that sets the stage for long-term success. By conducting a thorough market analysis, allocating resources efficiently, and developing accurate production forecasts, you can create a fabrikanlage that is not only productive and profitable but also adaptable to future market changes and technological advancements.
Optimizing Your Fabrikanlage for Peak Performance
Once your fabrikanlage is operational, the journey towards excellence doesn’t end. Continuous optimization is key to maintaining a competitive edge, reducing costs, and minimizing environmental impact. This ongoing process involves implementing lean manufacturing principles, adopting sustainable practices, and fostering a culture of continuous improvement.
Lean Manufacturing Principles: Eliminating Waste and Maximizing Value
Lean manufacturing is a methodology that focuses on eliminating waste and maximizing value in every aspect of the production process. By identifying and eliminating non-value-added activities, fabrikanlagen can streamline operations, reduce lead times, and improve overall efficiency.
Key lean manufacturing principles that can be applied to optimize a fabrikanlage include:
- Value Stream Mapping: This involves visualizing the entire production process from raw materials to finished products, identifying bottlenecks and areas for improvement.
- 5S Methodology: This system focuses on workplace organization and standardization, promoting a clean, efficient, and safe work environment.
- Just-in-Time (JIT) Production: JIT production involves producing goods only when they are needed, minimizing inventory costs and reducing waste.
- Kaizen: This Japanese term refers to continuous improvement, encouraging employees at all levels to identify and implement small, incremental improvements that can have a significant cumulative impact.
By embracing lean manufacturing principles, fabrikanlagen can achieve significant cost savings, improve product quality, and enhance customer satisfaction.
Sustainable Practices: Reducing Environmental Impact
Sustainability is becoming increasingly important in the manufacturing industry, and fabrikanlagen have a crucial role to play in reducing their environmental footprint. By adopting sustainable practices, fabrikanlagen can not only reduce their environmental impact but also improve their brand image and appeal to environmentally conscious consumers.
Key sustainable practices for fabrikanlagen include:
- Energy-Efficient Machinery: Investing in energy-efficient machinery and equipment can significantly reduce energy consumption and lower operating costs.
- Waste Reduction: Implementing waste reduction strategies, such as recycling, reuse, and source reduction, can minimize the amount of waste sent to landfills and reduce the need for raw materials.
- Renewable Energy: Exploring the use of renewable energy sources, such as solar or wind power, can help fabrikanlagen reduce their reliance on fossil fuels and lower their carbon emissions.
- Water Conservation: Implementing water conservation measures, such as recycling and reuse of water, can help fabrikanlagen reduce their water consumption and minimize their environmental impact.
By prioritizing sustainability, fabrikanlagen can contribute to a cleaner and healthier environment while also improving their bottom line.
Continuous Improvement: A Culture of Excellence
Continuous improvement is a mindset that permeates every aspect of a successful fabrikanlage. It involves a commitment to constantly seeking out ways to improve processes, products, and services. This can be achieved through regular data analysis, employee feedback, and a willingness to experiment with new ideas.
By fostering a culture of continuous improvement, fabrikanlagen can ensure that they remain at the forefront of innovation and efficiency. This not only benefits the company but also its customers, employees, and the environment.
Technology and Sustainability: The Twin Engines Driving Fabrikanlage Innovation
The modern fabrikanlage is a testament to the transformative power of technology and the growing commitment to sustainability in the manufacturing industry. These two forces are not only reshaping the way products are made but also redefining the very concept of the factory itself.
The Technological Impact on Fabrikanlage: A Revolution in Progress
Technological advancements are at the heart of the fabrikanlage revolution, driving unprecedented levels of efficiency, productivity, and innovation. Three key technologies are playing a pivotal role in this transformation: automation and robotics, IoT integration, and artificial intelligence.
Automation and Robotics: Streamlining Operations and Enhancing Productivity
Automation and robotics have become indispensable tools in modern fabrikanlagen, taking over repetitive, dangerous, and labor-intensive tasks. Robots can perform a wide range of functions, from welding and assembly to material handling and quality control. This not only frees up human workers to focus on more complex and creative tasks but also reduces errors, improves safety, and increases overall productivity.
IoT Integration: Creating a Connected and Intelligent Factory
The Internet of Things (IoT) is a network of interconnected devices that collect and exchange data. In a fabrikanlage, IoT devices can be embedded in machinery, equipment, and even products themselves. This allows for real-time monitoring of production processes, predictive maintenance, and data-driven optimization of operations. IoT integration enables fabrikanlagen to become “smart factories,” where data is used to make informed decisions, improve efficiency, and enhance product quality.
Artificial Intelligence: Empowering Decision-Making and Problem-Solving
Artificial intelligence (AI) is revolutionizing the way fabrikanlagen operate by enabling machines to learn from data, identify patterns, and make intelligent decisions. AI-powered systems can optimize production schedules, predict equipment failures, and even design new products. By leveraging AI, fabrikanlagen can become more agile, adaptable, and responsive to changing market conditions.
Sustainability in Fabrikanlage: A Commitment to a Greener Future
Sustainability is no longer a buzzword but a core principle that guides the design and operation of modern fabrikanlagen. This commitment to environmental responsibility is driven by a growing awareness of the impact of manufacturing on the planet and a desire to create a more sustainable future.
Eco-Friendly Manufacturing Techniques: Minimizing Environmental Impact
Fabrikanlagen are increasingly adopting eco-friendly manufacturing techniques that minimize waste, reduce energy consumption, and conserve resources. This includes the use of recycled materials, water-saving technologies, and energy-efficient processes. By minimizing their environmental footprint, fabrikanlagen can contribute to a cleaner and healthier planet.
Energy Efficiency: Reducing Consumption and Costs
Energy efficiency is a top priority for fabrikanlagen, as it not only reduces their environmental impact but also lowers operating costs. This is achieved through a combination of measures, such as investing in energy-efficient machinery, optimizing energy use, and implementing energy management systems. By reducing their energy consumption, fabrikanlagen can become more sustainable and cost-competitive.
Circular Economy: Closing the Loop on Resources
The circular economy is a model of production and consumption that aims to minimize waste and make the most of resources. In a fabrikanlage, this can be achieved by designing products for durability and repairability, reusing and recycling materials, and recovering energy from waste. By adopting circular economy principles, fabrikanlagen can reduce their reliance on virgin materials, minimize waste, and create a more sustainable manufacturing ecosystem.
Global Trends Revolutionizing the Fabrikanlage Landscape
The evolution of the fabrikanlage is far from over. It is continually being shaped by global trends that are transforming the manufacturing industry, pushing the boundaries of innovation, and redefining the way we produce goods. These trends, including Industry 4.0, global supply chains, and green manufacturing, are not only reshaping the physical and technological aspects of fabrikanlagen but also influencing their strategic role in the global economy.
Industry 4.0: The Digital Transformation of Fabrikanlagen
Industry 4.0, also known as the Fourth Industrial Revolution, is a technological revolution that is transforming the manufacturing industry through the integration of digital technologies, data analytics, and automation. For fabrikanlagen, this means a shift towards smart factories that are interconnected, data-driven, and highly automated.
Smart Factories: The Future of Manufacturing
In the Industry 4.0 era, fabrikanlagen are evolving into smart factories where machines, systems, and products communicate with each other in real-time. This interconnectedness allows for unprecedented levels of data collection and analysis, enabling predictive maintenance, real-time optimization of production processes, and improved decision-making.
Digital Twins: Virtual Replicas for Optimization
Digital twins are virtual replicas of physical assets, such as machines, equipment, or even entire fabrikanlagen. By simulating and analyzing the behavior of these assets in a virtual environment, manufacturers can optimize their performance, predict failures, and test new ideas before implementing them in the real world.
Additive Manufacturing: Revolutionizing Production
Additive manufacturing, commonly known as 3D printing, is another key technology that is transforming fabrikanlagen. By enabling the production of complex parts and prototypes on demand, additive manufacturing is revolutionizing the way products are designed and manufactured, reducing lead times, and enabling greater customization.
Global Supply Chains: A Complex Network of Interdependencies
The globalization of manufacturing has led to the creation of complex and interconnected supply chains that span the globe. Fabrikanlagen are increasingly becoming integral nodes in these networks, sourcing materials and components from various locations and shipping finished products to markets worldwide.
Supply Chain Resilience: Mitigating Risks and Ensuring Continuity
The COVID-19 pandemic exposed the vulnerabilities of global supply chains, highlighting the need for greater resilience. Fabrikanlagen are now focusing on building more resilient supply chains that can withstand disruptions and ensure the continuity of operations. This involves diversifying suppliers, building buffer stocks, and implementing robust risk management strategies.
Supply Chain Optimization: Leveraging Data and Technology
Fabrikanlagen are increasingly using data analytics and digital technologies to optimize their supply chains. This includes tracking shipments in real-time, predicting demand fluctuations, and optimizing inventory levels. By leveraging these tools, fabrikanlagen can reduce costs, improve delivery times, and enhance customer satisfaction.
Green Manufacturing: A Sustainable Approach to Production
The growing awareness of environmental issues and the increasing demand for sustainable products are driving a shift towards green manufacturing. Fabrikanlagen are at the forefront of this movement, adopting eco-friendly practices and technologies to minimize their environmental impact.
Resource Efficiency: Minimizing Waste and Maximizing Resource Utilization
Green manufacturing emphasizes resource efficiency, aiming to minimize waste and maximize the utilization of resources such as energy, water, and raw materials. This can be achieved through various measures, such as recycling, reuse, and the adoption of energy-efficient technologies.
Renewable Energy: Reducing Reliance on Fossil Fuels
Many fabrikanlagen are exploring the use of renewable energy sources, such as solar and wind power, to reduce their reliance on fossil fuels and lower their carbon footprint. This not only contributes to environmental sustainability but can also reduce energy costs in the long run.
Circular Economy: Closing the Loop on Resources
The concept of the circular economy is gaining traction in the manufacturing industry. It involves designing products for longevity, reusing and recycling materials, and minimizing waste. Fabrikanlagen are increasingly adopting circular economy principles to reduce their environmental impact and create a more sustainable manufacturing ecosystem.
Conclusion
The dawn of the Fabrikanlage era signifies a transformative shift in the manufacturing landscape, promising a future brimming with possibilities. As we navigate the complexities of the 21st century, the fabrikanlage stands as a beacon of innovation, adaptability, and resilience. It is a testament to human ingenuity and our relentless pursuit of progress in the realm of production.
The path forward for fabrikanlagen is paved with technological advancements that will continue to redefine the boundaries of what is possible. From artificial intelligence and machine learning to the Internet of Things and robotics, these technologies will empower fabrikanlagen to become even more intelligent, efficient, and responsive to the ever-changing needs of the market.
But the future of the fabrikanlage is not just about technology. It is also about adapting to the dynamic nature of global markets and evolving consumer preferences. The ability to pivot quickly, customize products, and optimize supply chains will be crucial for fabrikanlagen to maintain their competitive edge in a world of constant change.
The role of the fabrikanlage in the future of manufacturing is undeniable. It is not merely a place where goods are produced but a hub of innovation, collaboration, and sustainable practices. Fabrikanlagen are poised to become the backbone of a new industrial revolution, one that prioritizes efficiency, quality, and environmental responsibility.
As we look ahead, it is clear that the fabrikanlage is more than just a manufacturing plant; it is a symbol of progress, a testament to human ingenuity, and a beacon of hope for a more sustainable and prosperous future. By embracing technological advancements, adapting to market changes, and prioritizing sustainability, fabrikanlagen will continue to play a pivotal role in shaping the future of manufacturing.
You May Also Like
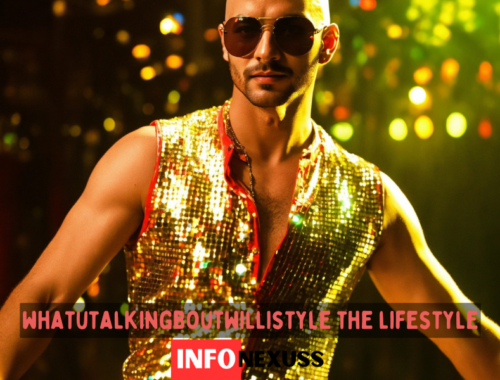
Your Guide to Whatutalkingboutwillistyle the lifestyle
June 7, 2024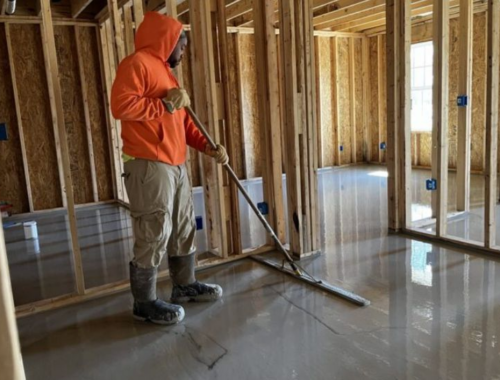
7 Reasons To Install Gypcrete Under Your House
October 31, 2024